V industriji granulacije, ne glede na to, ali gre za stroj za pelete z ravnim ali obročastim peletnim strojem, je njegovo načelo delovanja, da se zanaša na relativno gibanje med tlačnim valjčkom in kalupom, da zgrabi material in vstopi v učinkovito postajo, ga iztisne v obliko in ga nato z rezilom razreže na delce zahtevane dolžine.
Lupina valja za stiskanje delcev
Ohišje pritisnega valja vključuje predvsem ekscentrično gred, kotalne ležaje, ohišje pritisnega valja, ki je nameščeno zunaj gredi pritisnega valja, in komponente, ki se uporabljajo za podporo in pritrditev ohišja pritisnega valja.
Pritisni valj stisne material v odprtino kalupa in ga pod pritiskom oblikuje v odprtini kalupa. Da bi preprečili zdrs pritisnega valja in povečali silo prijema, mora obstajati določena sila trenja med pritisnim valjem in materialom. Zato se na površini pritisnega valja pogosto izvajajo ukrepi za povečanje trenja in odpornosti proti obrabi. Pri določanju strukturnih parametrov pritisnega valja in kalupa imata strukturna oblika in velikost zunanje površine pritisnega valja pomemben vpliv na učinkovitost granulacije in kakovost delcev.
Površinska struktura lupine pritisnega valja
Za obstoječe valje za stiskanje delcev obstajajo tri običajne vrste površin: žlebljena površina valja, žlebljena površina valja z robnim tesnjenjem in satasta površina valja.
Pritisni valj z zobatim utorom ima dobro kotalno zmogljivost in se pogosto uporablja v tovarnah krme za živino in perutnino. Vendar pa zaradi drsenja krme v zobatem utoru obraba pritisnega valja in obročastega kalupa ni zelo enakomerna, obraba na obeh koncih pritisnega valja in obročastega kalupa pa je močnejša.
Pritisni valj z zobatim utorom in robnim tesnjenjem je primeren predvsem za proizvodnjo vodnih materialov. Vodni materiali so med ekstrudiranjem bolj nagnjeni k drsenju. Zaradi robnega tesnjenja na obeh straneh zobatega utora se material med ekstrudiranjem ne premika proti obema stranema, kar ima za posledico bolj enakomerno porazdelitev materiala. Obraba pritisnega valja in obročastega kalupa je prav tako bolj enakomerna, kar ima za posledico bolj enakomerno dolžino proizvedenih peletov.
Prednost satjastega valja je v enakomerni obrabi obročastega kalupa in relativno konstantni dolžini proizvedenih delcev. Vendar pa je delovanje tuljave slabo, kar vpliva na izhod granulatorja in ni tako pogosto kot uporaba reže v dejanski proizvodnji.
Sledi povzetek 10 vrst tlačnih valjev za stroje za delce za kalupe tlačnih valjev Baoshell, zadnje 3 pa zagotovo še niste videli!
ŠT. 10 Vrsta utora
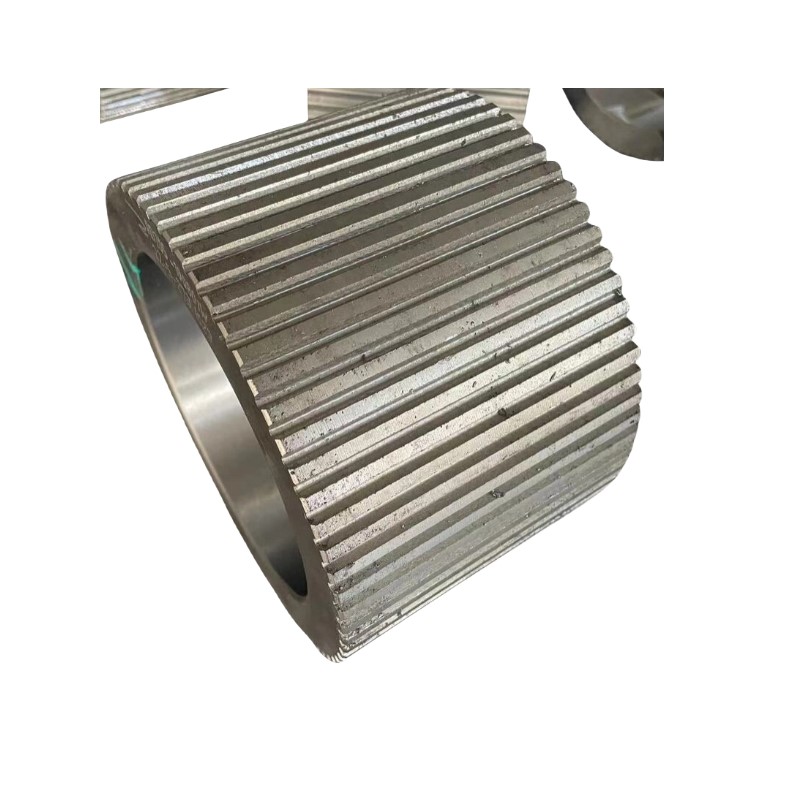
ŠT. 9 Zaprti utor
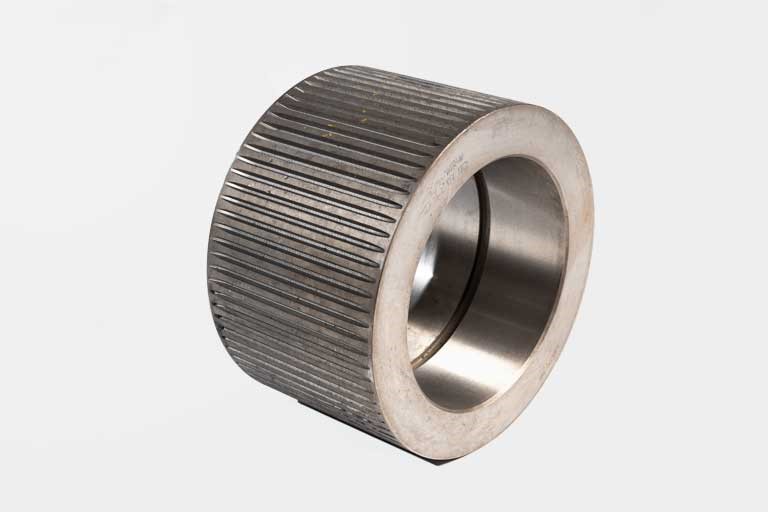
ŠT. 8 Vrsta satja
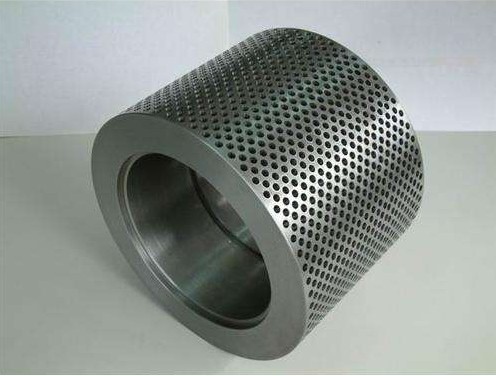
ŠT. 7 V obliki diamanta
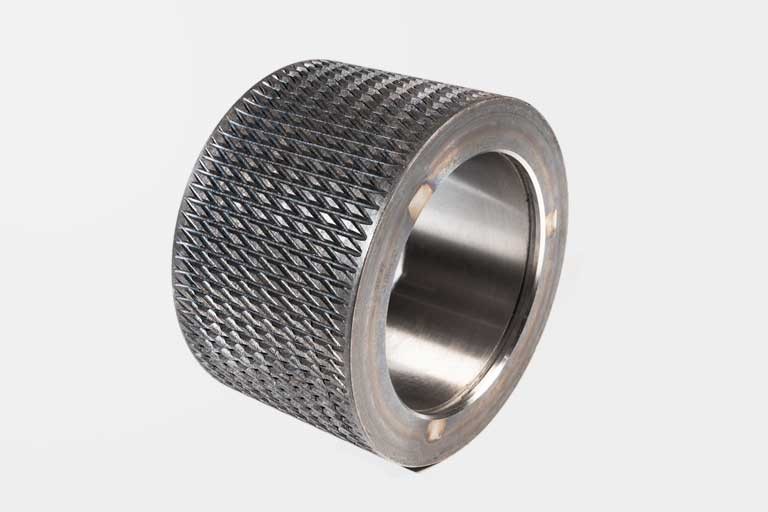
ŠT. 6 Nagnjeni utor
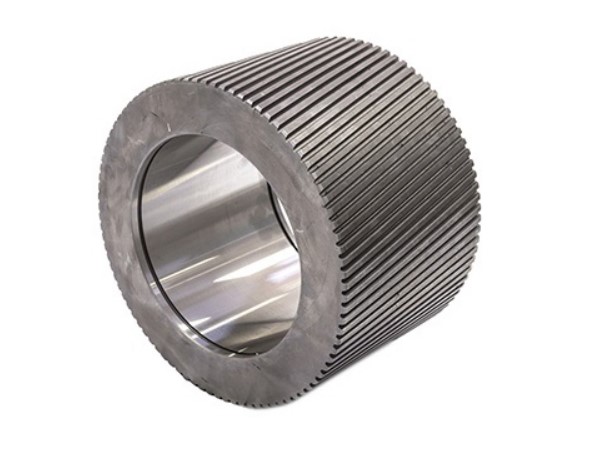
ŠT. 5 Utor + satje
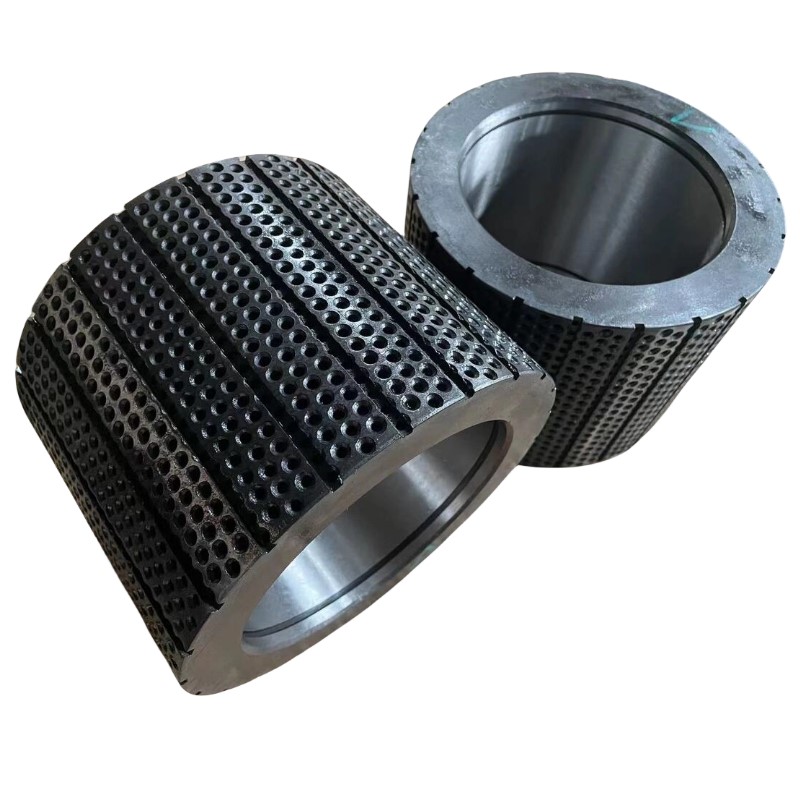
ŠT. 4 Zaprti utor + satje
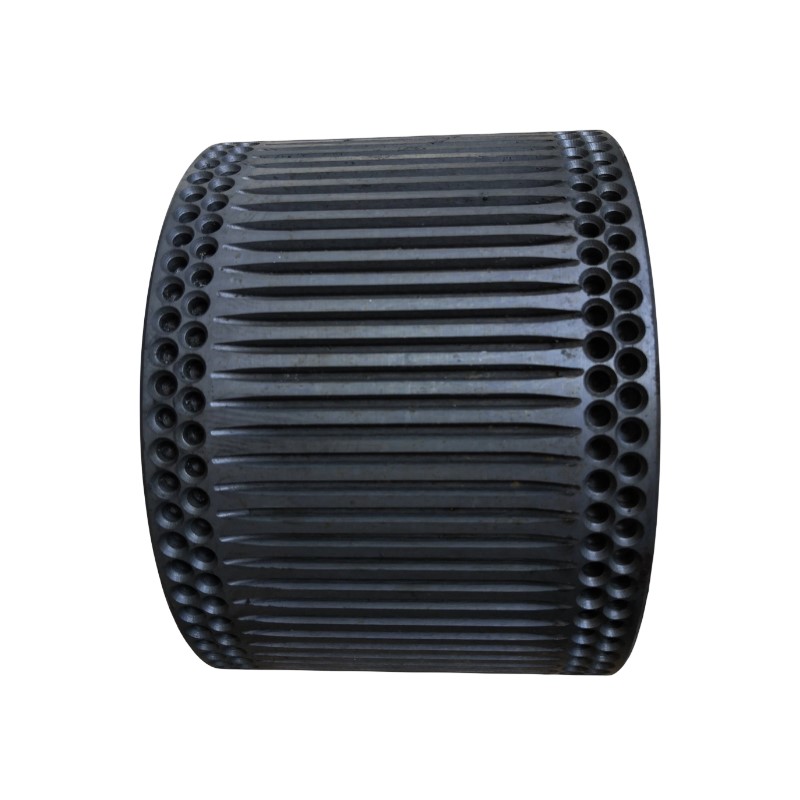
ŠT. 3 Nagnjen utor + satovje
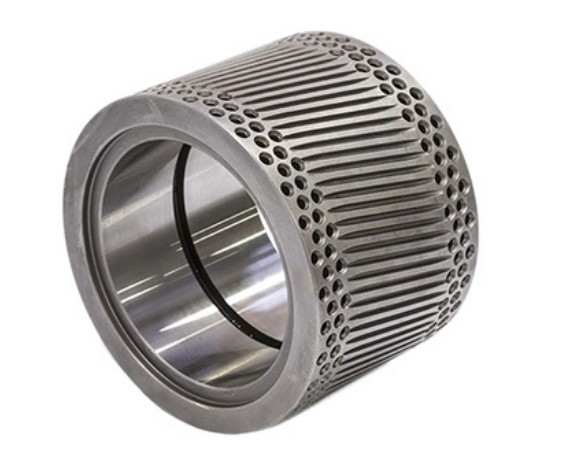
ŠT. 2 Valovanje ribje kosti
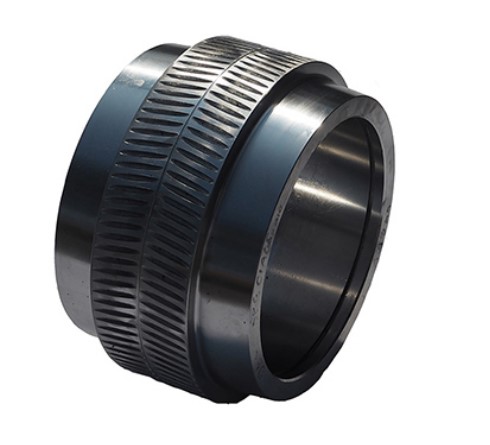
ŠT. 1 Valovanje v obliki loka
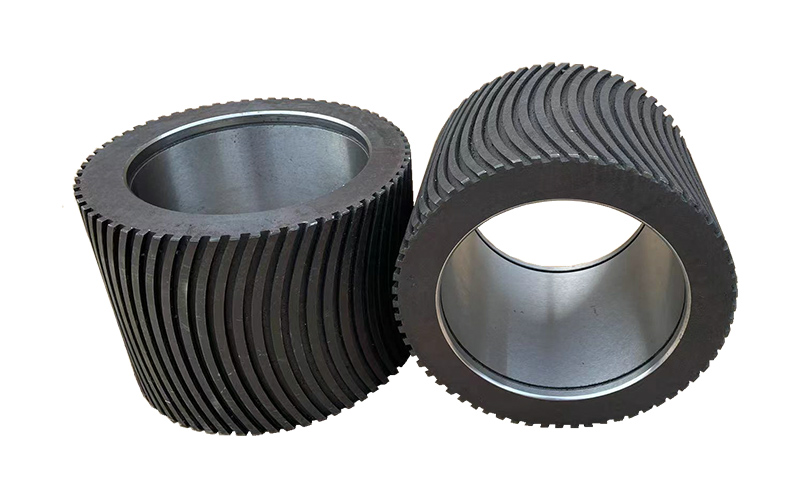
POSEBNI MODEL: OKOLIŠČE IZ VOLFRAMOVEGA KARBIDNEGA METALA
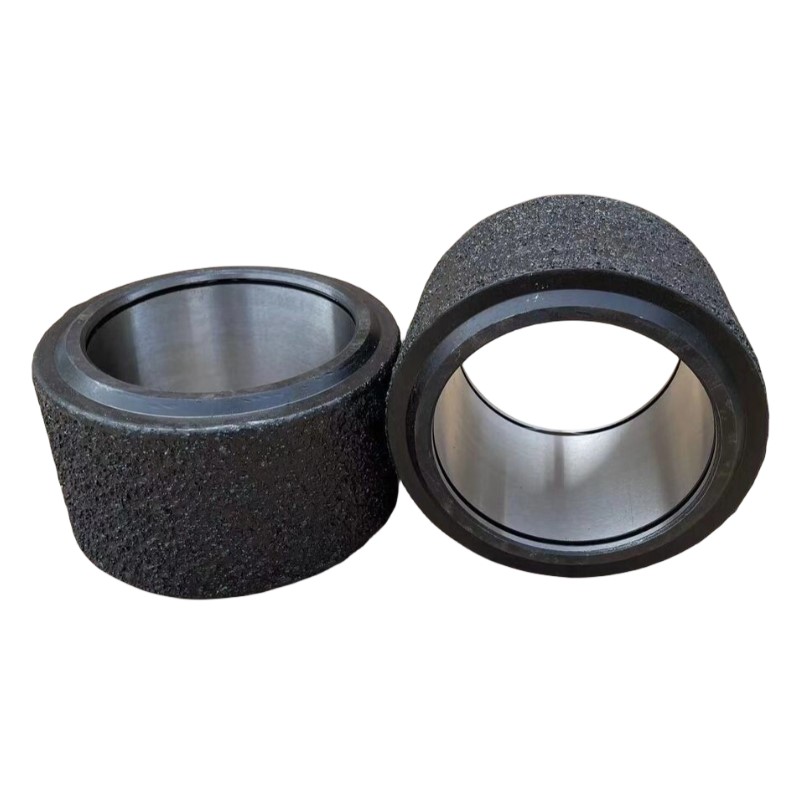
Metoda obdelave za zdrs pritisnega valja stroja za delce
Zaradi zahtevnega delovnega okolja, visoke delovne intenzivnosti in hitre obrabe ohišja pritisnega valja je pritisni valj ranljiv del stroja za delce in ga je treba redno menjati. Proizvodna praksa je pokazala, da lahko pride do zdrsa pritisnega valja stroja za delce, če se lastnosti proizvodnih materialov ali drugi pogoji med obdelavo spremenijo. Če med postopkom granulacije pride do zdrsa pritisnega valja, ne paničarite. Za podrobnosti glejte naslednje tehnike:
Razlog 1: Slaba koncentričnost pritisnega valja in namestitve vretena
Rešitev:
Preverite, ali je namestitev ležajev pritisnih valjev smiselna, da se prepreči odklon ohišja pritisnega valja na eno stran.
Razlog 2: Zvonasta odprtina obročnega kalupa je zravnana, zaradi česar kalup ne je materialov
Rešitev:
Preverite obrabo sponk, pogonskih koles in obložnih obročev granulatorja.
Prilagodite koncentričnost namestitve obročnega kalupa z napako, ki ne presega 0,3 mm.
Razmik med pritisnimi valji je treba nastaviti tako, da: polovica delovne površine pritisnih valjev deluje s kalupom, kolo za nastavitev razmika in zaklepni vijak pa morata biti tudi v dobrem delovnem stanju.
Ko pritisni valj zdrsne, ne pustite stroja za delce delovati predolgo v prostem teku in počakajte, da sam izprazni material.
Kompresijsko razmerje uporabljene odprtine obročnega kalupa je previsoko, kar povzroča visok upor pri izpustu materiala iz kalupa in je tudi eden od razlogov za zdrs pritisnega valja.
Stroja za pelete ne smete pustiti v prostem teku brez dovajanja materiala.
Razlog 3: Ležaj tlačnega valja je zataknjen
Rešitev:
Zamenjajte ležaje tlačnih valjev.
Razlog 4: Ohišje pritisnega valja ni okroglo
Rešitev:
Kakovost ohišja valja ni ustrezna, zamenjajte ali popravite ohišje valja.
Ko pritisni valj zdrsne, ga je treba pravočasno ustaviti, da se izognemo dolgotrajnemu trenju pritisnega valja v prostem teku.
Razlog 5: Upogibanje ali zrahljanje vretena pritisnega valja
Rešitev:
Zamenjajte ali privijte vreteno in pri zamenjavi obročnega kalupa in pritisnega valja preverite stanje vretena pritisnega valja.
Razlog 6: Delovna površina pritisnega valja je relativno neusklajena z delovno površino obročnega kalupa (prekrižanje robov)
Rešitev:
Preverite, ali je pritisni valj nepravilno nameščen, in ga zamenjajte.
Preverite, ali je ekscentrična gred pritisnega valja deformirana.
Preverite obrabo ležajev ali puš glavne gredi stroja za delce.
Razlog 7: Zračnost vretena granulatorja je prevelika
Rešitev:
Preverite pritezno zračnost granulatorja.
Razlog 8: Stopnja prebijanja obročnega kalupa je nizka (manj kot 98 %)
Rešitev:
Za vrtanje skozi luknjo v kalupu uporabite vrtalnik s pištolo ali pa ga skuhajte v olju in ga pred hranjenjem zmeljete.
Razlog 9: Surovine so pregrobe in imajo visoko vsebnost vlage
Rešitev:
Pazite na vzdrževanje vsebnosti vlage približno 15 %. Če je vsebnost vlage v surovinah previsoka, bo prišlo do blokade kalupa in zdrsa po vstopu surovin v obročasti kalup. Razpon nadzora vlage v surovinah je med 13 in 20 %.
Razlog 10: Prehitro hranjenje nove plesni
Rešitev:
Prilagodite hitrost, da zagotovite zadosten oprijem pritisnega valja, preprečite zdrs pritisnega valja in pravočasno preverite obrabo obročnega kalupa in pritisnega valja.
Čas objave: 25. marec 2024